O que acontece dentro da rosca com o sólido compactado?
- Cassiana Assis
- 28 de jan. de 2023
- 3 min de leitura
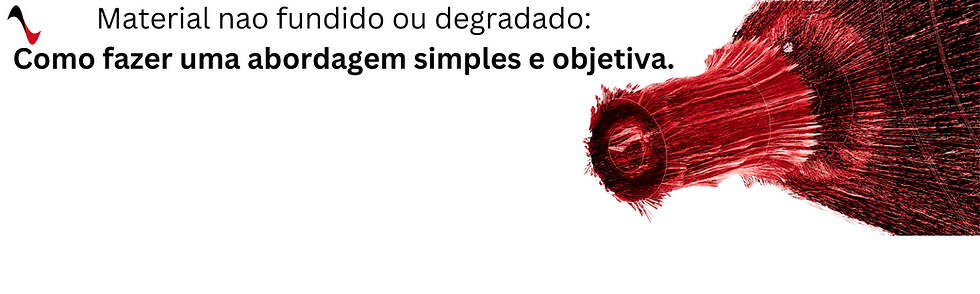
Desde 1960 um trabalho extensivo tem sido realizado para se explicar como o polímero é processamento dentro da extrusora. O método desenvolvimento por Tadmor e Klein em 1970 é o mecanismo de fusão. A matemática proposta nos dá uma visão bem elaborada da geometria da rosca, das condições operacionais e das propriedades termo físicas do polímero analisado.
A figura 01 ilustra a transformação de um polímero dentro de uma extrusora padrão. A rosca ilustrada possui um perfil típico, com três zonas (alimentação, compressão e fusão, homogeneização). Os peletes do polímero são introduzidos ao funil e transferidos por gravidade para dentro da rosca. O material polimérico continua a ser transportado pela ação do fluxo de arraste até o início do processo de fusão, resultado do aquecimento do cilindro e da energia mecânica dissipada pelo atrito gerado. O mecanismo de fusão segue uma lógica bem sequenciada e vai processasse ao longo da rosca.
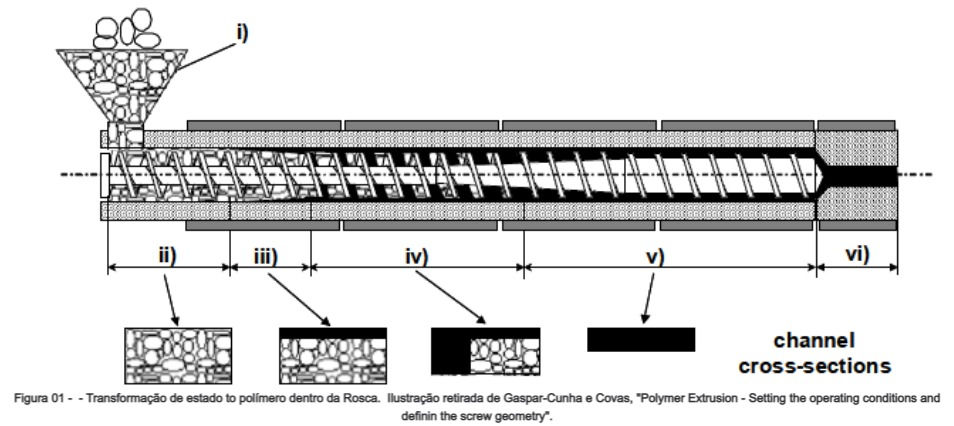
O extrudado começa a fundir nas paredes internas do cilindro e começa a formar a piscina do fundido (melt pool) e o sólido compactado (solid bed). A figura 2 ilustra esta primeira etapa no processo de fusão.

Uma camada fina de polímero fundido pode acontecer nas paredes da superfície da rosca, gerando as espessuras δ1,δ2 e δ3, assim como ilustrado na Figura 03.

Várias pesquisas experimentais demonstraram que os passos para a fusão do material polimérico são afetados pelas condições operacionais, pelas propriedades do material e pela geometria da rosca.
Sendo assim, é possível descrever o processo de plastificação em 6 zonas funcionais:
O transporte de sólidos (i. na figura 01) ou peletes dentro do funil.
O fluxo de arraste de sólidos (ii. na figura 01), nos diâmetros iniciais da rosca.
O Atraso no processo de fusão (iii. na figura 01). Gerado por camada fina de material fundido (figura 03) que envolve o sólido compactado (solid bed), retardando a fusão por evitar o contacto direto com as paredes metálicas e reduzir o atrito.
Fusão (iv. na figura 01).
Transporte de fundido (v. na figura 01)
Fluxo da matriz (vi. na figura 01)
Eficiência do processo de fusão ao longo da Rosca.
A eficiência da fusão ao longo da rosca é avaliada entendendo-se qual o percentual de material não fundido. Isso permite avaliar qual o percentual na ponteira da rosca, no quebra-fluxo ou na matriz. Na figura 2, podemos observar que a largura total do filete da Rosca "W" e a largura de sólido compactado "X".
A razão de material não fundido pode ser expressada por X/W. Este conhecimento permite que ao se projetar a rosca ou avaliar um material em processamento, se reflita na necessidade de se instalar elementos de mistura.
Precisar o local e seu impacto no produto extrudado, evita sobre aquecimentos ou o déficit na eficiência em fundir o material.
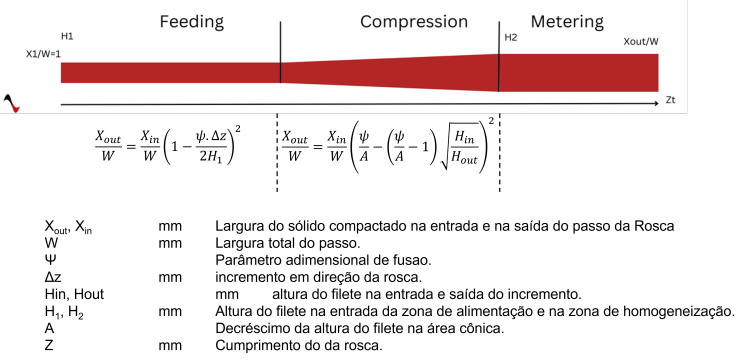
Figura 04 -Descrição do perfil de fusão do material polimérico em uma rosca de três zonas.
Segundo a Figura 4, podemos separar uma rosca típica de 3 zonas. Com uma precisão aceitável, adota-se uma metodologia simples para observar o comportamento do polímero ao durante seu processamento.
Analisando a base da rosca e classificando-a em duas espécies: cilíndrica e cônica. Na região cilíndrica são observadas as zonas de alimentação e homogeneização. A região cônica, observa-se a zona de compressão. Para se estimar o percentual de material sólido ou fundido, podemos utilizar as equações também ilustradas na Figura 04.
Naturalmente, a metodologia proposta é uma abordagem rápida e simples para uma primeira avaliação. A Figura 05 ilustra os resultados desejados ao longo da rosca. A curva verde, é o primeiro parâmetro a ser observado, calculado quando a extrusora estiver em seu regime de produção máximo.

Figura 05 - Comportamento de perfil de sólido fundido, pressao do material e temperatura ao longo da rosca em regime de producao máximo.
De acordo com a prática e uma série de trabalhos realizados pela #pdcaepbrasil e outros autores, esta análise permite otimizar o processamento o material à condições existentes máquina, ao minimizar risco de processo e recursos empregados. Ademas, quanto maior sintomia entre operadores, líderes de produção sobre o equipamento, material e processo, maiores as chances de sucesso. .
Confira também nosso artigo que explica simulação de processo.
Esperamos que tenham gostado deste artigo. Ficamos à disposição de perguntas, sugestões e comentários. Não perca seu foco.
Cassiana Assis, Gerente Geral, PDCA Extrusion Processing.
Esperamos seu contato:
+49 173 360 2430 / cassiana.assis@pdcaextrusion.com
+21 98028 1816 / domingos.savio@pdcaextrusion.com
O material extrudado está degradado ou não está bem fundido?
Degradado ou queimado
Não foi inteiramente fundido ou plastificado dentro da rosca

Comentários